December 11, 2018
Ultra-sized Panel System
Product sizes are usually limited by the market available metal sheet sizes. However, by utilizing Kikukawa’s various welding technologies (such as FSW and laser welding), Kikukawa is able to fabricate extremely wide or long panels. Kikukawa’s new limitations are transportation, lifting load, and installation conditions.
As Kikukawa’s system relies on the combination of factory welding, and on-site welding, Kikukawa is able to fabricate and install extremely large (ultra-sized) panels. This fabrication system is achievable by considering and reflecting the following specifications to the design drawings; from the selection of the thickness of the material to the interlaminar distortion level, and the calculation of thermal expansion upon welding, to the transportation and installation sequence.
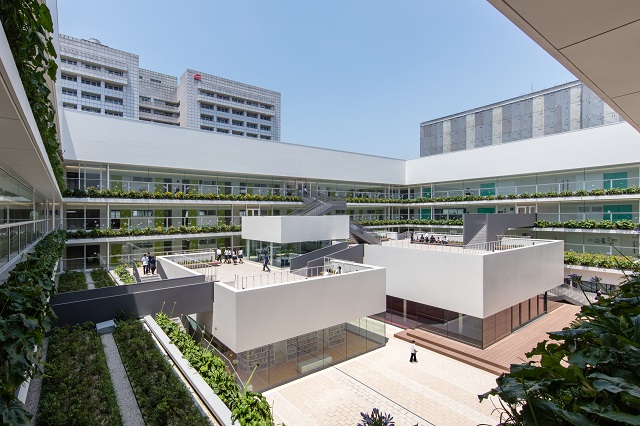
Each face of the building within this courtyard is installed as a single panel
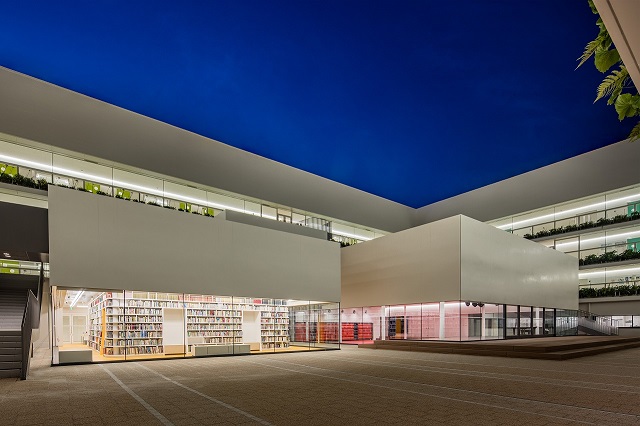
The only visible joints are at the corners, emphasizing the extreme sizes of the panels
The exterior of the buildings in the courtyard, library and multi-purpose room of this high school reflects the designer intent to fabricate each face of the building in a one-panel unit.
The panels are made of 12mm thick steel sheets, hot-dip galvanized then painted with fluororesin coating. (Different paint was used for on-site paint coating.) Roughly 400 square-meters of exterior panels consist of 15 panels, with the maximum size being 18m wide and 4m high.
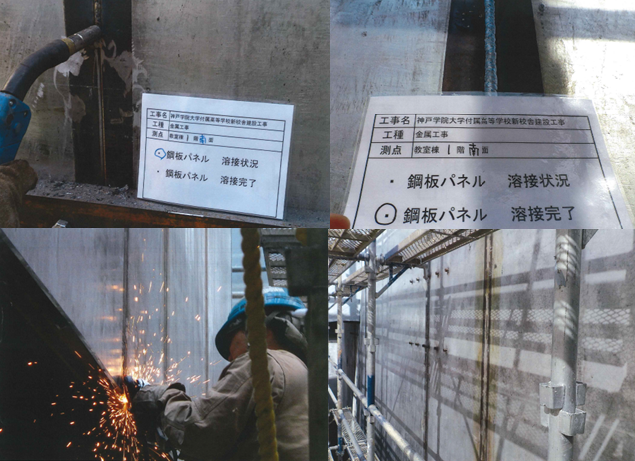
Welding and finishing the panels on-site
To fabricate these ultra-sized panels, 9 shop-welding and 14 on-site welding were conducted. Typically, distortions from the welding do not allow for on-site welding for facade panels. However, Kikukawa calculated these risks and implemented strongback frames, as well as careful considerations in the welding procedure to minimize distortion.
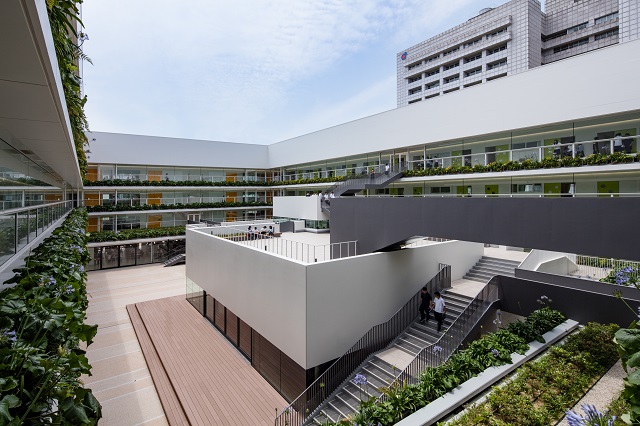
Regardless of the shape or the adjoining fixtures details, each face consists of a single extremely large panel
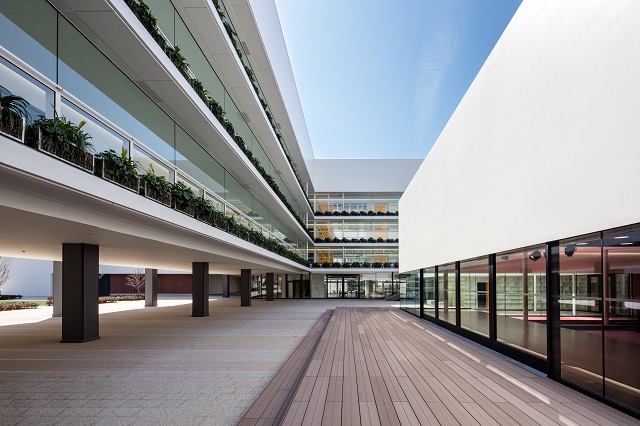
18m wide and 4m high panels, fabricated with the ultra size panel system
Demands for jointless products are increasing, and to respond to these needs, Kikukawa will continue to challenge the limitations of extremely wide or long panels.
For more information on FSW, one of Kikukawa’s welding technology, click here
For more information on extremely wide or long panels, click here