Mirror Finish
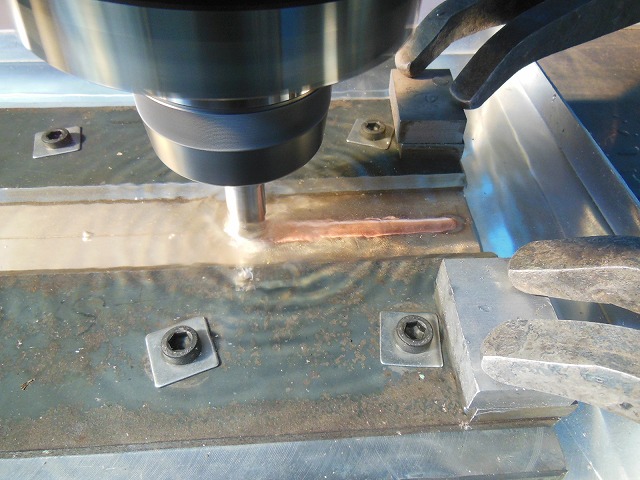
FSW in process
FSW (Friction Stir Welding) is a solid-state joining process that uses frictional heat and mechanical mixing process to achieve high quality and high strength joints over conventional welding processes. The workable sheet metals are aluminium up to 10mm thickness, copper alloy up to 6mm and magnesium up to 10mm in 1 pass. The maximum workable size is 2800mm(W) x 4000mm(L), however, the maximum product size can be negotiated by adjusting the fixtures. This technology can be used to fabricate extra-wide or extra-long sheet metals, flat-surfaced extrusions, or 2D curved welds. Benefits over conventional processes include high weld strength and minimal distortion due to the low heat and small heat-affected area. At KIKUKAWA, further research on dissimilar metal welds or applications with other metal-crafting technology is being explored.
Click here to view our brochure on ‘FSW (Friction Stir Welding)’
Main Features | -Stronger welding joints compared to conventional welding -Capable of fabricating sheets larger than the standard market dimensions -Clean welding method that produces little dust, fumes, or other hazardous substances -Long welding -Flat Curved Welding |
---|---|
Name/Type | Friction Stir Welding (FSW) |
Applicable Materials | -Aluminium 1.5~10.0mm -Bronze Alloy 1.5~6.0mm -Magnesium 1.5~10.0mm *These are figures based on 1 pass |
Categories | -Welding sheet metals with minimal deformation -Extra-long metal sheets or products -Welding extrusion -Able to accommodate small lots of a high-variety product lines -Curved welding |
Maximum Workable Size | 2800mm(W) x 4000mm(L) *Please consult us for any products over this size |
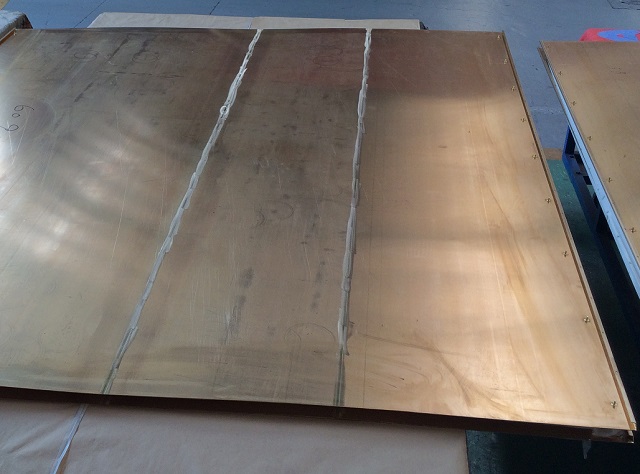
Three Bronze Sheet Metals, FSW
■What is Friction Stir Welding?
The Friction Stir Welding, FSW, is a process that joins two workpieces without melting the materials. A rotating cylindrical tool is pressed against the surfaces and moved along the joint. The frictional heat and mechanical mixing process generated by the moving tool causes the stirred materials to plasticize (soften) and join without melting.
Patented in the 1990s, this leading welding technology continues to be researched and experimented for further applications.
■Advantages of Friction Stir Welding
FSW offers significant benefits over conventional welding processes, especially for flat surfaces.
1. High Weld Strength
In comparison to conventional fusion-welding processes such as arc welds, FSW joints result in a fine grain structure that resists fatigue stress. This superior mechanical characteristic translates to minimal distortion (shrinkage or cracking) and minimal porosity in the joined parts.
2. High Quality
-Minimal Distortion / Deformation
Unlike conventional welding that relies on high temperature to melt the surfaces, FSW relies on low heat and it only affects a small area. This means that the FSW joints have minimal distortion and/or deformation. Our study found that the rate of distortion of a FSW joint is a fraction of a TIG welded joint.
-Minimal Decolouration
Unlike TIG welds or even laser welds, the surface of FSW joints has fewer flaws such as beads or discoloration from the heat. The high-quality welding is especially evident once the product is complete as it directly affects the overall physique. For instance, the welding joint would be unnoticeable once the bronze is finished with sulfurization.
3. A Green Process
In comparison to conventional processes, FSW is a more environmentally friendly option. The welding does not produce sputter or fumes that are toxic. It also does not use consumables such as filler materials or shielding gases.
4. Auto Features
With the NC control and KIKUKAWA’s expertise, the machine could adjust the levels as needed to ensure precision. The machine could also read 3D CAD files, enabling curved welds.
■Applications of FSW
Given the high strength, minimal deformation and minimal decolouration characteristics of FSW welds, here are some examples of its application.
1. Fabrication of extra-wide/extra-long metal sheets (over market size)
-Two 1200×3000 metal sheets welded to fabricate a 2400×3000 sheet
-Three 1200×3000 metal sheets welded longitudinally to fabricate a 1200×9000 sheet
2. Welding Extrusions
-Two 50x150x4000 square pipes welded to fabricate a 50x300x3000 pipe
-Two 50x150x4000 square pipes welded to fabricate a 50x150x8000 pipe
3. Minimizing loss rate of metal sheets
-Welding 300(W) and 200(W) end materials to fabricate a 500(W) sheet
The FSW welding can accommodate small lots, thus is suitable for experimenting, or for sample fabrications.
KIKUKAWA offers other metal-crafting services in addition to the FSW, expanding the possibilities of feasible designs.
■Finding Solutions
With the development of 3D CAD and fabrication technology, the complexity and diversity of architectural designs continue to expand. As a bespoke architectural metalworker, we are often consulted on their feasibility, such as “minimal joints” or “3D curvatures”.
To respond to the changing demand, KIKUKAWA introduced the FSW machine.
■Contact Us
As one of the latest welding technology, studies on FSW continue to expand. At KIKUKAWA, research and experimentation on FSW and its combination with other metal-crafting technology are being explored. Our services range from product fabrication that was previously difficult, to bending or perforating after welding.
From consultation to fabrication feasibility, please do not hesitate to contact us.
For more information on metalworking capabilities, click here
Custom Metalwork
To make an inquiry, click here
Contact Us
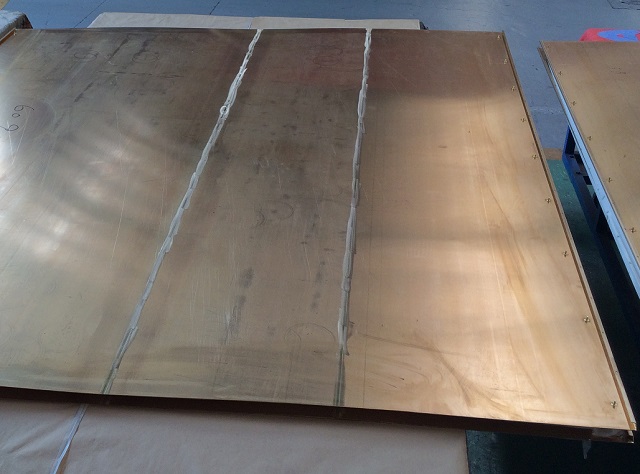
Three Bronze Sheet Metals, FSW
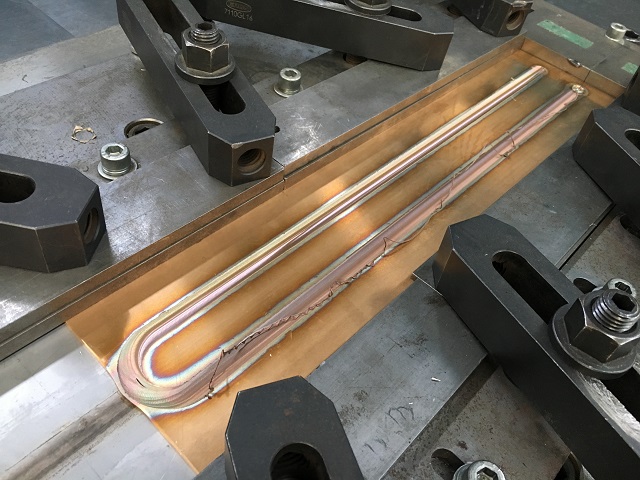
FS welding long distance, and in curves
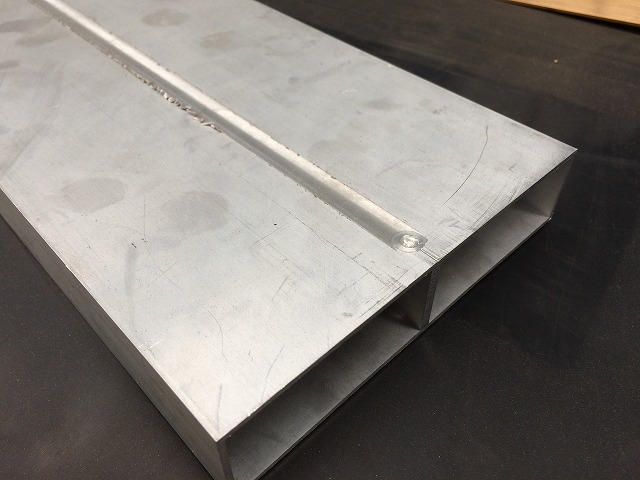
FSW Extrusion
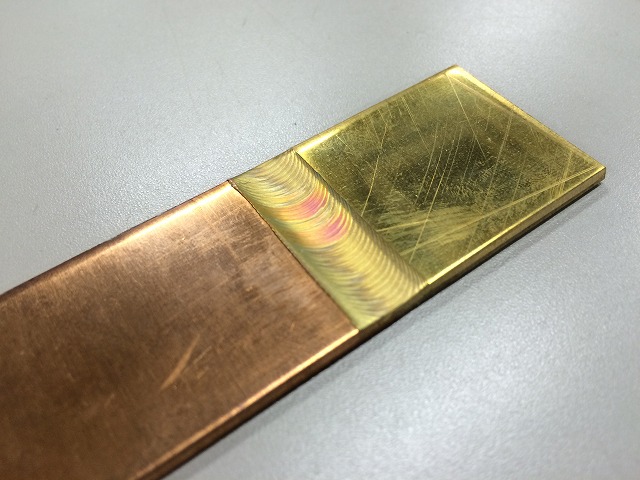
FSW, Dissimilar Metals