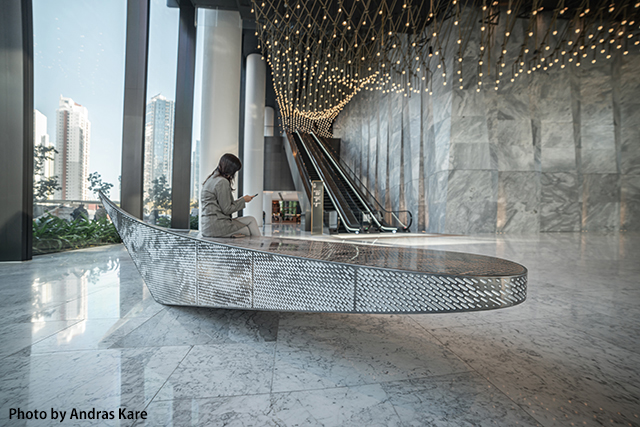
The Kai Tak Turn bench, crafted in aluminum alloy
The bench’s dynamic form was achieved through using metalworking techniques to create curves
Milling technology formed the grooves which make up the patterns on the panel surfaces
■International Project: Fabricating an Aluminum Alloy Bench for a Multi-Use Building
AIRSIDE is a large multi-use complex, housing both a shopping mall and office space, in Hong Kong. It was built on the site of the city’s former Kai Tak Airport. The complex features a number of sculptures throughout the site. KIKUKAWA was involved in the production of one of them, an aluminum alloy bench given the name ‘Kai Tak Turn’ designed by miriamandtom.
―Kai Tak Turn is one in a series of commissioned sculptures located throughout Airside that is conceived of a marriage between Fabric and Flight – ‘Fabric’ being Nan Fung’s history in the textile trade and ‘Flight’ being Kai Tak’s history as an airport.
(Cited from miriamandtom’s website)
■Achieving Curves through Substrate Structure and Bending Technology
The bench is approximately 1.2m in depth, 4.4m in width, and 1m in height. It is comprised of 22 aluminum alloy panels, welded together to form a single object. The ends of the bench float, unsupported, in the air; in fact, they are supported by the structure at the center. The seating area has a gentle upwards curve.
―Its form and aluminium construction references aviation wings and the fluidity of its surface references the movement of fabric in the wind.
(Same as above)
Kai Tak Airport was renowned for the so-called Hong Kong Approach, where landing aircraft were required to perform sharp turns at low altitude over the Hong Kong skyline. The bench was designed to evoke this iconic maneuver.
KIKUKAWA studied a number of internal structural designs to achieve the desired shape and strength. Ultimately, we settled on a lattice structure that follows the bench’s curved surface. This enabled us to seamlessly position and fit the decorative panels.
Roll bending technology was used to form the surface of the curved seating area. Skilled craftsmanship contributed to achieving the desired curve, making minute adjustments along the way as required. Fibre laser welding was chosen for the panel joints, as it results in fine yet deep welds. This allowed us to maximise the area left for decorative patterning.
Click here to find out more about Fibre Laser Welding
■Patterns Created by Milling Technology
The bench was crafted in 4mm thick aluminum alloy (A5052). This material is renowned for being both resistant to corrosion and exceptionally strong, which is why it is often used in machining applications. Among a number of surface finishing options we proposed, the client chose the milling method.
The patterning – inspired by clouds seen from above – consists of grooves milled into the panel surface. These grooves are between 3mm to 30mm in length and 1mm to 2mm in depth. By varying the length and depth, we were able to create an effect similar to cloud gradients seen in satellite imagery. It is an attractive design that changes dramatically depending on whether it is being viewed up close or from afar.
Using milling technology for this type of surface finishing was a challenge for KIKUKAWA, so an extensive process of trial and error was necessary to decide upon the final process. Our efforts included the careful examination of the usage of milling machine itself, and test milling was conducted at increments of 0.1mm. Ultimately, we were able to create this decorative finishing product for our client.
After milling, the panels underwent blasting and were then finished by hand using PHL (vibration). This skillful craftsmanship resulted in an impeccable finish, with just the right amount of shine.
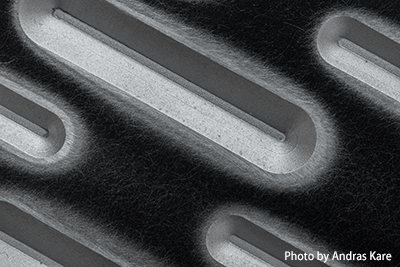
▲A close-up of the surface finishing reveals intricate craftsmanship
■KIKUKAWA’s Metalworking Expertise and Craftsmanship
Both machining processes using digital technology, like milling and fibre laser welding, and traditional craftsmanship only possible by expert hand, like bending and polishing, are aspects indispensable in metalworking today. This project represented the successful integration of uniquely delicate Japanese metalworking techniques with our monozukuri approach to craftsmanship: creating quality through continuous improvement. We are incredibly proud to have been able to create a superb product that embodies our approach to an international client.
Product | Material | Metal Finishes or Metalwork |
---|---|---|
Bench "Kai Tak Turn" |
Aluminum Alloy | Fibre Laser Welding Milling Bead Blasting / PHL |
Project | AIRSIDE, “Kai Tak Turn” |
---|---|
Client | Nan Fung Group |
Architect | Design: miriamandtom Design and Engineering Consultant: VIA/FRONT |
Completion | 2023 |
Location | Hong Kong |