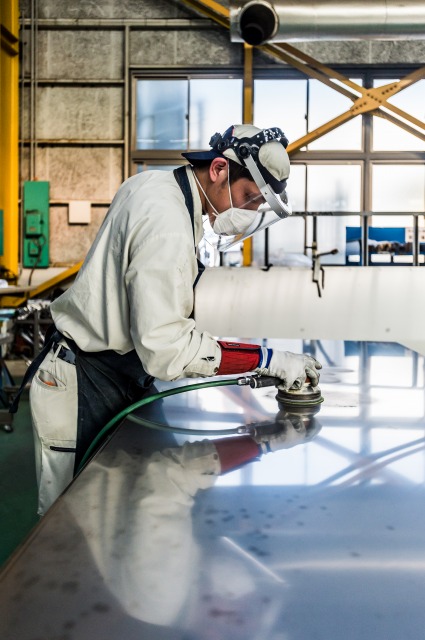
Kikukawa's craftsman preparing the base material with hand polishing
Polishing or grinding finish is a type of surface finish applied by utilizing various abrasive machining processes. The grinding patterns vary depending on the material, polisher, finishes and the patterns. These patterns and finishes can be mix-and-matched, applied in layers or designed freely, thus allowing greater freedom in architectural designs.
Polishing or grinding as a machining process is used in various industries from small parts of precision instruments to large products such as an aircraft.
Within metal architecture, polished or grinding finish has been selected for various places from curtain walls, interiors and exteriors, fittings, and monuments for its ability to accommodate various designs.
At Kikukawa, we have the expertise and technology, and established partnerships to provide high-quality polished finish as required by the project. We accommodate copper alloys (copper, bronze, brass), aluminium, and stainless steel products up to 1500mm (W) by 6000mm (L), although accommodated size depends on the material, material thickness, shape, and the polishing patterns.
Main Features | ・High-quality polished finish offered with extensive experience in quality control ・Various polishing patterns accommodated ・Bespoke polishing finishes and development of new polishing finishes accommodated ・Large panels accommodated ・Oleophobic coating or passivation coating accommodated ・Combinations with other finishes accommodated ・Finish that enhances the material |
---|---|
Applicable Materials | ・Aluminium ・Copper alloys (copper, bronze, brass) ・Stainless steel ・Other metals |
Maximum Workable Size | ・Extra-wide panels over 1500mm (W) ・Extra-long panels over 6000mm (L) *Panels over this size are also accommodated upon request, however limitations depend on material thickness and size of the product. Please consult us for details. |
Remarks | As Kikukawa is an expert in architectural metal constructions and metal works, we do not accommodate requests that only require a polished finish. |
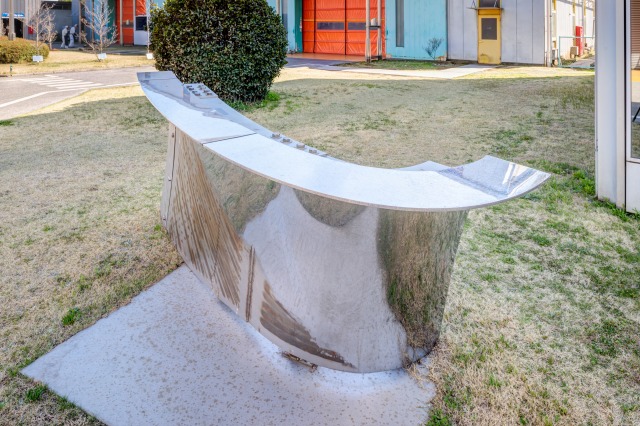
Left: Stainless steel after welding. Right: Stainless steel, welded and finished with mirror polish and pearl vibration
■What is polishing or grinding finish?
Polishing or grinding typically refers to the abrasive machining process but polishing or grinding finish refers to a patterning process applied as a surface finish. The variations in the final pattern depend on factors such as the workpiece material, grinding material, polisher, patterns, and the variations of the patterns’ width, length, direction, shape or depth. This variation and the resulting texture expands when combined with other surface finishes. As a finish that enhances the beauty of the material that can fully utilize the properties of metal, and provides a wide variety of design options, it continues to be favored by many designers.
■Purpose of polishing or grinding finish
Within architecture, polishing or grinding finish has been favored as a finish that could utilize the advantageous properties of the material and for its design flexibility.
The origin of polishing or grinding finish is the machining process of the same name. Grinding is used for various materials from metal, stones, and wood to attain the desired surfaces. To achieve the required functionality or aesthetics, grinding or polishing can smooth or roughen the surface, or adjust the surface in a matter of millimeters.
For metal architecture, grinding or polishing finish is used to adjust the quality of the surface, the adjustment of corrosion resistance after welding, to improve the slipperiness of the pieces, to improve the shine, and for other aesthetics. Aesthetic surface finishes include HL (hairline), PHL (permanent hairline), bead-blasting and mirror-polish.
■Applying the grinded or polished finish within metal architecture
Adjusting the surface of the material can be accomplished mechanically or chemically. Chemical polishing is achieved by dipping the workpiece into chemical solutions and is known as etching or electro-polishing. Mechanical polishing relies on a tool and a liquid polisher such as sanding papers, polishing stones and polishing papers. Application of this technique can achieve bead-blasted finish or mirror-polished finish.
Grinded or polished finish are often automated however certain workpieces require polishing by hand, such as the edges of workpieces, dual-curved pieces or pieces that have already been metalwork-ed (bent or welded).
■Considerations when choosing polished or grinded finish
Grinded or polished finish is popular in various designs for various uses, however, please consider the following prior to its selection as a surface finish.
◇With metal, polished surfaces are susceptible to distortion. For projects or works with strict flatness requirements, correctional measures are necessary.
◇As grinded finishes fully utilize the beauty of the material, the resulting polish marks or patterns depend on the quality of the original surface material. Thus factors such as the lot of the material, or the components of the alloy may need to be coordinated.
◇Polished finishes such as mirror finishes may result in the surfacing of small holes that were present in the material, known as pits or pinholes. Upon discovery of these imperfections, re-polishing of the material is required.
■Kikukawa’s polished or grinded finish
At Kikukawa, we provide polished or grinded finish as required by the project. Applicable materials are aluminium, stainless steel and copper alloys (copper, bronze, and brass). Please consider 1500mm (W) and 6000mm (L) as a benchmark for accommodated sizes. As Kikukawa selects the most suitable polishing methodology per the requirement of the project, accommodated sizes or applicable polishing marks may change. Please consult us prior to your final selection.
◇Oleophobic coating
Grinded metal surfaces has minimal dents or protrusions from the abrasions and are prone to fingerprints. Kikukawa is able to apply oleophobic coating without interrupting the texture of the surface. As the coating protects the material from fingerprints or dirt marks, the maintenance of the material becomes easier.
◇Passivation coating
Passivation is a naturally occurring protective coat that forms on the surface of stainless steel that protects it from corrosion. This coat forms when chromium within the material is exposed to air. The layer is extremely thin but is chemically stable, thus is able to reform when damaged.
This coat is interrupted when polished. In order to enjoy the surface finish for a larger period of time, Kikukawa is able to artificially apply this coat.
◇Bespoke or developed finish, and combination with other finishes
In addition to regular HL (hairline) or PHL (permanent hairline) polished finish, Kikukawa is able to combine other finishes or develop bespoke finishes or patterns. Adjusting the coarseness, depth, and frequency, or application of repeating the polishing marks (such as cross HL) are accommodated. Additionally, combinations with other finishes are available.
Consider the following examples. With aluminium, anodization, etching or electro-finishing, of polished surfaces are available. For stainless steel, sputtering or colouring the grinded finish could achieve a textured surface. With copper alloys, sulfurization and clear coating the material may be considered.
Other designs include partial application of polishing finishes, or changing the direction of polishing patterns. A simple change in the direction of polishing creates a variation in colour from varying reflections.
Kikukawa is able to develop new polishing patterns or new finish samples based on the design intent or ideas.
To view the aluminium finish samples, click here
To view the stainless steel finish samples, click here
To view the bronze finish samples, click here
For more information on bead-blasting, click here
Metal Craft News: Copper Artwork Enhanced with Multiple Finishes
◇Outsized metal products
Polished or grinded finished extra-wide or extra-long claddings are accommodated. Kikukawa has a vast factory and facilities to metalwork these outsized materials and claddings as needed. Additionally, the procurement of high-quality outsized materials is possible.
Kikukawa’s experience includes 18.5m bead-blasted facade of 8m round column covers.
To view Kikukawa’s projects with outsized cladding, click here
To learn more about Kikukawa’s technology on outsized cladding, click here
■On-site welding and polishing
Typically, the polishing finish is applied within the factory for consistency and quality control. However, certain projects (such as the outsized cladding) require on-site welding or on-site polishing.
Kikukawa is able to provide on-site welding with small welding beads with minimal distortion.
This is especially useful for large monuments that require large-scale welding and polishing on-site.
Consider, for instance, the Yaesu central ventilation tower of Tokyo station. The requirements of the shell-shaped monument were 17,000mm in length, 6,700mm in width, 4,800mm in height, a singular self-standing unit. The shell is composed of 24 pieces of 9mm stainless steel, welded and pearl vibration finished on-site.
Another example would be of a certain high-end retail brand store formed with 111 claddings that were welded on-site then partially mirror polished. The largest panel is 2,000mm (W) and 10,000mm (H) and the requirements included leaving the welding bead. This project was accomplished by quality controlling the entire process from the procurement to planning installation, and consultations in detailed designing.
For more information on Yaesu central ventilation tower of Tokyo station, click here
For pictures of pearl vibration finish, click here
◇Kikukawa’s quality control
Kikukawa has the technology and quality control know-how to provide high-quality facade panels. With polished finish, the quality of the material and the handling of the material defines the final quality of the product – Kikukawa has the expertise to control these conditions.
■Examples of Kikukawa’s polished finish, and projects with polished (grinded) finish
◇HL (hairline) finish
One of the classic polished finishes characterized by long, continuous and uni-directional grind marks. Adjustments of this finish result from changing the application methodology or the applicator to adjust the grind size, depth, direction or continuity.
To view projects with HL (hairline) finish, click here
◇PHL (permanent hairline) finish
Another classic polishing finish characterized by non-directional arches. The grind size and depth can be adjusted.
To learn more about the PHL (permanent hairline) finish, click here
To view projects with PHL (permanent hairline) finish, click here
◇PVIB (pearl vibration) finish
A beautiful finish characterized by numerous circular grind marks.
To view projects with PVIB (pearl vibration) finish, click here
◇Mirror polished finish
This finish is obtained by repeatedly polishing the workpiece, switching from coarse grinding paper to finer grinding paper until there are no visible grind marks. Therefore, polished finish that lies somewhere in between the base material to the mirror-polished finish can be accommodated. As this finish reflects any imperfections such as scratches, pinholes, or deflections, the level of difficulty in metalworking and installing the product is high.
To view projects with mirror polished finish, click here
◇Bead blasted finish (Silky Blast)
Blasting is a surface finish or treatment obtained by the impact of various blast media (materials) propelled onto the surface of sheets or products. By elevating this finish with its proprietary technology and know-how, Kikukawa provides the ‘Silky Blast’ finish.
To learn more about the bead blasting and Silky Blast finish, click here
To view projects with bead-blasted finish, click here
◇Electropolishing
The surface is polished by immersing the workpiece into an electrolyte and passing a current. An application of this is used to achieve the bright dip anodized aluminium.
To view projects with bright dip anodized aluminium, click here
◇Etching
The polishing is achieved by chemically processing the workpieces.
◇Custom (bespoke) designs
As Kikukawa specializes in bespoke architectural metalworking and facade constructions, we are able to provide consultations for new designs from feasibility to sample fabrications. Our past experience includes partial polishing or patterning, based on varying polishing marks and directions.
Here is an excerpt of custom-designed grinded finishes.
・Cross HL (hairline)
・Scratch HL (hairline)
・Kishage (blocks of varying polishing marks on a mirror-polish)
・Hand polishing
■Please consult us
Kikukawa provides a variety of polished finish metal architectural constructions.
Depending on the material, or the polishing patterns such as its depth, direction, continuity or width, and by combining multiple polishing patterns and other surface finishes, the achievable design intents are endless.
Please consult us on the feasibility, samples or designs of polished (grinded) finish.
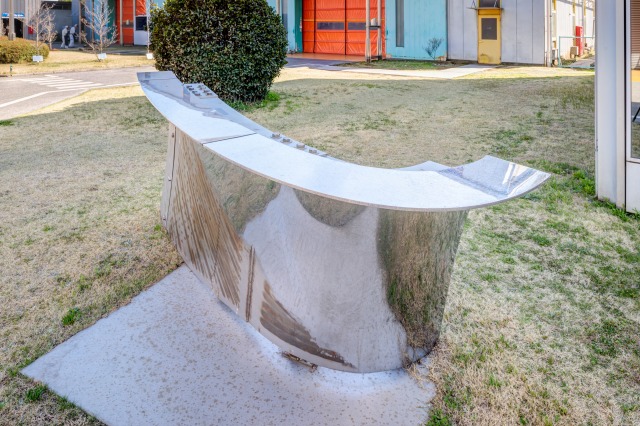
Left: Stainless steel after welding. Right: Stainless steel, welded and finished with mirror polish and pearl vibration
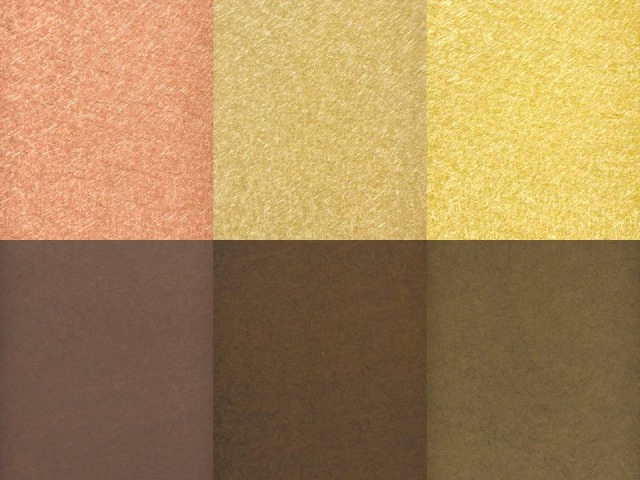
Kikukawa's polished copper alloy samples. Top row from the left: PHL finished copper, bronze, and brass. Bottom row from the left: PHL and lightly sulfurized copper, bronze, and brass. The same polishing pattern creates a wide range of textures depending on the material and the surface finish.
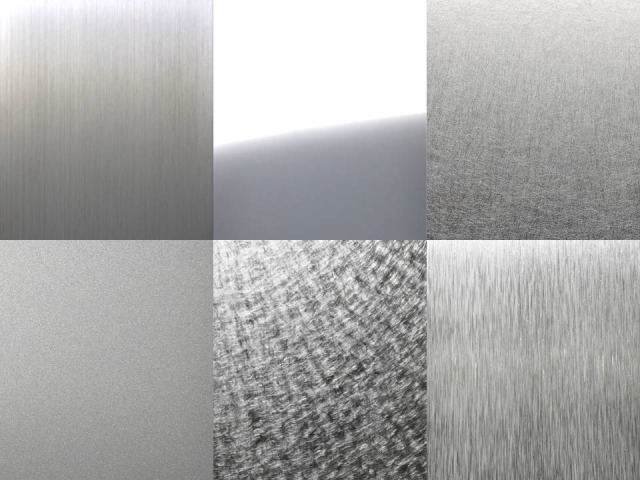
Common stainless steel polished finishes. Clockwise from the top left: HL, mirror polished, PHL, scratch HL, pearl vibration and Silky Blast.
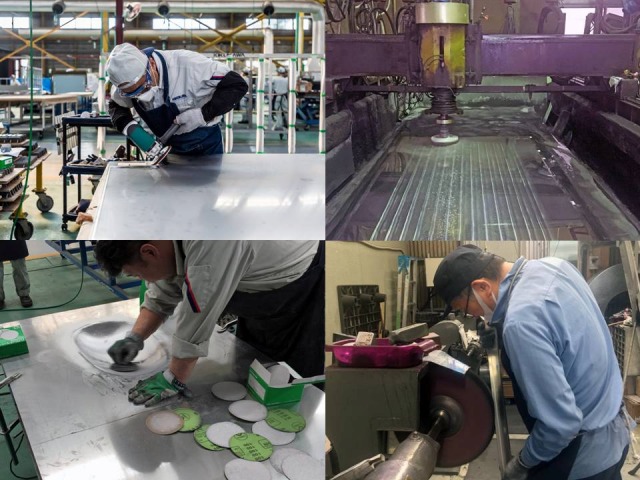
Depending on the material and shape, the most suitable polishing methodology is chosen. Clockwise from the left: finishing the edges, mirror polishing with a machine, hand polishing long bars, and hand polishing of a double curved product.