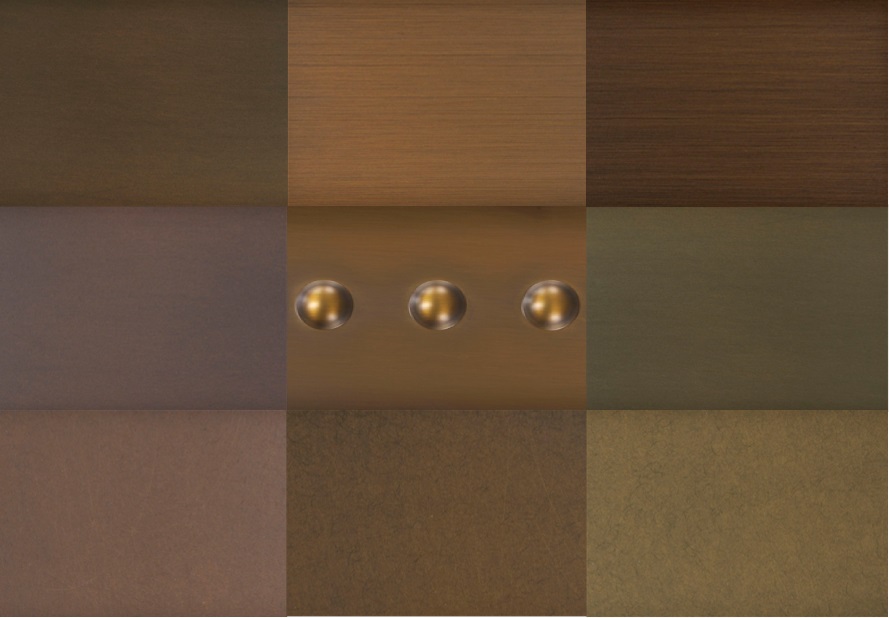
KIKUKAWA's Sulfurized Bronze Finish
Sulfurization is a process that recreates the rich brown hues of patinated copper alloy that would otherwise take decades to form. The classic artisanal finish allows for the creation of a calming and stately space – which explains its popularity for uses in museums, public facilities, historical and religious architecture.
Main Features | -Tone adjustments possible -Two types of sulfurization; dry and wet -High-quality finish ensured with skilled craftsmanship and quality management system |
---|---|
Applicable Materials | Copper Alloy -Brass -Bronze -Copper |
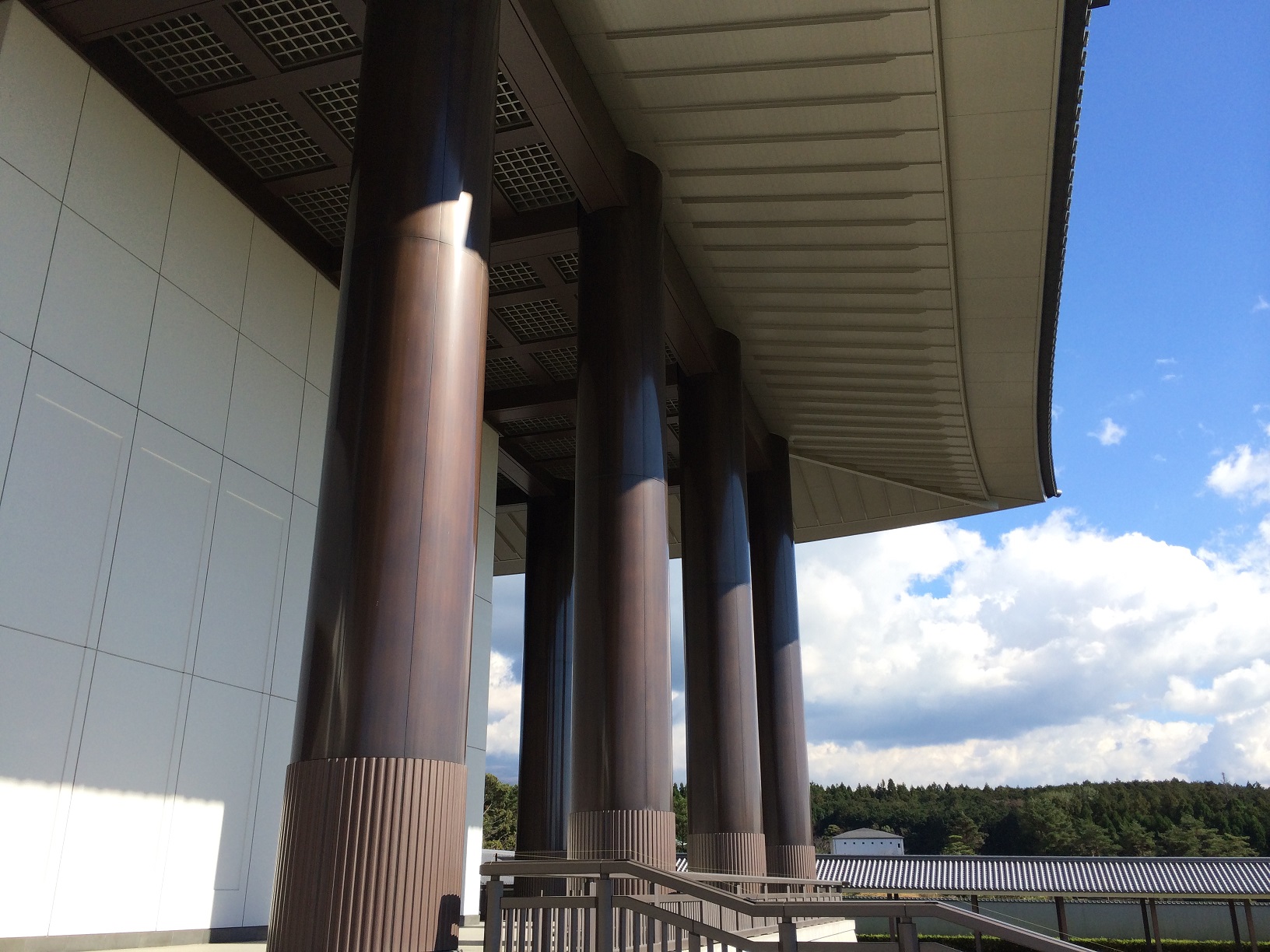
Sulfurized Round Columns
■Overview of the Sulfurization Finish
Sulfurization, an artisanal finish applicable to various copper alloys (copper, bronze, brass), recreate the rich brown hues of oxidated (patinated) copper alloys.
In nature, copper alloys darken over time with exposure to the atmosphere, a process known as oxidation. A common example would be the Japanese 10yen coin (or consider a penny) – the new coins yield a shiny pink tone yet settles to a brown tone over time. Similarly, bronze architectural materials settle from a high sheen to varying shades of brown, to green patina.
Sulfurization is a technique that chemically fastens this oxidation process.
The sulfurization finish is popular within and out of the country as the resulting tone contributes to the creation of a luxurious, stately yet warm space.
■On Copper Alloys
Traditionally, copper alloys have been favoured in architecture for its physique and properties (waterproof and corrosion resistant) in various uses. The high workability of the metal added to its convenience, for fabrications of complex shapes. Even today, other properties, such as its anti-bacterial nature, makes this material subject of research for further uses as an architectural material.
By mix and matching various finishes, copper alloys can realize a wide range of design intents. For instance, mirror polished brass alloys add a luxurious sheen to the space with its gold-like texture. Hammered (Tsuchime) copper alloys used in kitchens contribute to a playful atmosphere for its resemblance to hammered cookware.
■Process of Sulfurization Finish
There are two types of sulfurization processes – dry and wet. The appropriate process is selected depending on the size, shape and finishing tone required.
The main difference comes from the state of the formula – powder or liquid – and its application process – powdered or dipped -. In both cases, both pieces are finished one by one at Kikukawa.
■Kikukawa’s Sulfurization Finish
- 1. Quality Management
The process of patination is an art as much as it is science.
The difficulty of sulfurization finish stems from its unique shade. In nature, the varying hues stem from the property of the material or the surfacace condition, and exterior factors such as weather, moisture content or traffic.
At Kikukawa, the quality of the finish is ensured through a sulfurization process line that is overseen by a management system, as certified by ISO9001, and with expertise.
- 2. Developing the FURUMI (sulfurized) Finish
Kikukawa is committed to producing high-quality bespoke products as needed. – and finishes are no exceptions.
FURUMI (sulfurization) finish is a Kikukawa original that was developed specifically for Cathay Pacific. From a single photo, Kikukawa fabricated over 100 sample pieces to realise the tone imagined and were highly regarded for its commitment and work.
From new projects to reconstruction projects, Kikukawa has the expertise and craftsmanship to actualise what is needed.
- 3. Fabrication size
Cutting-edge technology such as FSW (Friction Stir Welding) and Fiber Laser Welding, allows fabrication from small pieces to pieces that are over market-available sizes.
■Considerations when using Sulfurization
The finishing process is an art as much as it is a science and craftsmanship; the effect of the sulfurization process is highly dependent on ambient conditions (such as the weather or humidity) as well as the chemical composition or the lot of the material. This ambiance is widely understood as part of the beauty of sulfurization finish.
At Kikukawa, dry sulfurized products are shipped with a coat of clear coating. The purpose is to protect the brown hues of the sulfurized finish from the initial risks of peeling or spotting rather than to retain its colours for years. These considered risks stem from the products being handled and moved during shipment and installation.
For example:
-The clear coating protects the sulfurized finish from direct contact during installation that could lead to inconsistency in the oxidized tone.
-The peeling or chipping of sulfurization resulting from inconsistency in the amount of powder that remained on the surface of the product.
Underneath the coat of clear coating, the sulfurized products continue to slowly and naturally oxidize and by the time the effects of clear coating diminishes, the hues settle to a rich brown tone.
At Kikukawa, a finish sample is produced to ensure the consistency of the tone required.
■Please Consult Us
Sulfurization is a process that recreates the brown hues of patination that occurs over time and one that recreates its unique tone. For feasibility of a particular tone or possibility of further metalwork, please do not hesitate to contact us.
For more information on Kikukawa’s bronze finishes, click here
Kikukawa’s Bronze Finish Samples
To make an inquiry, click here
Contact Us
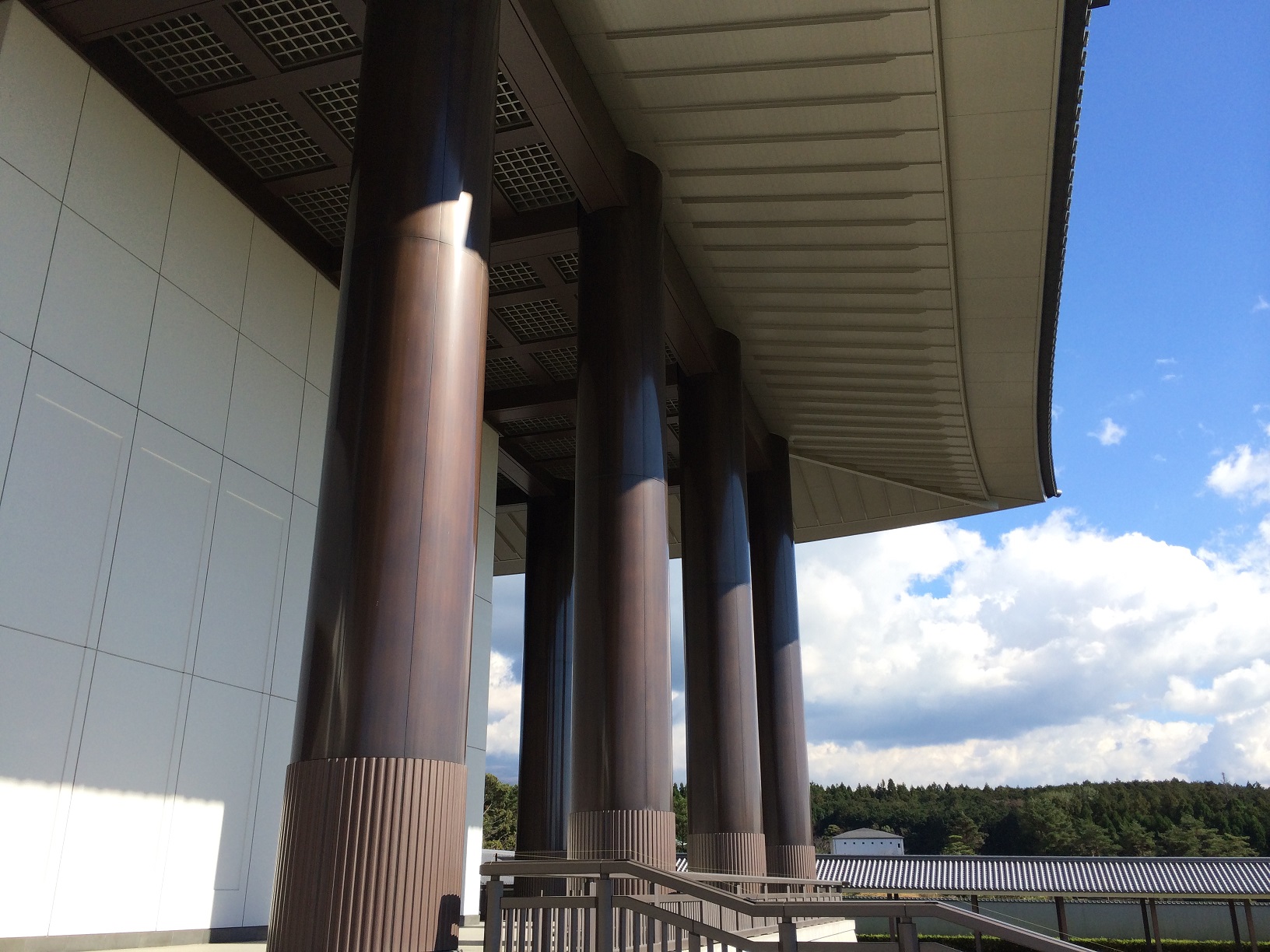
Sulfurized Round Columns
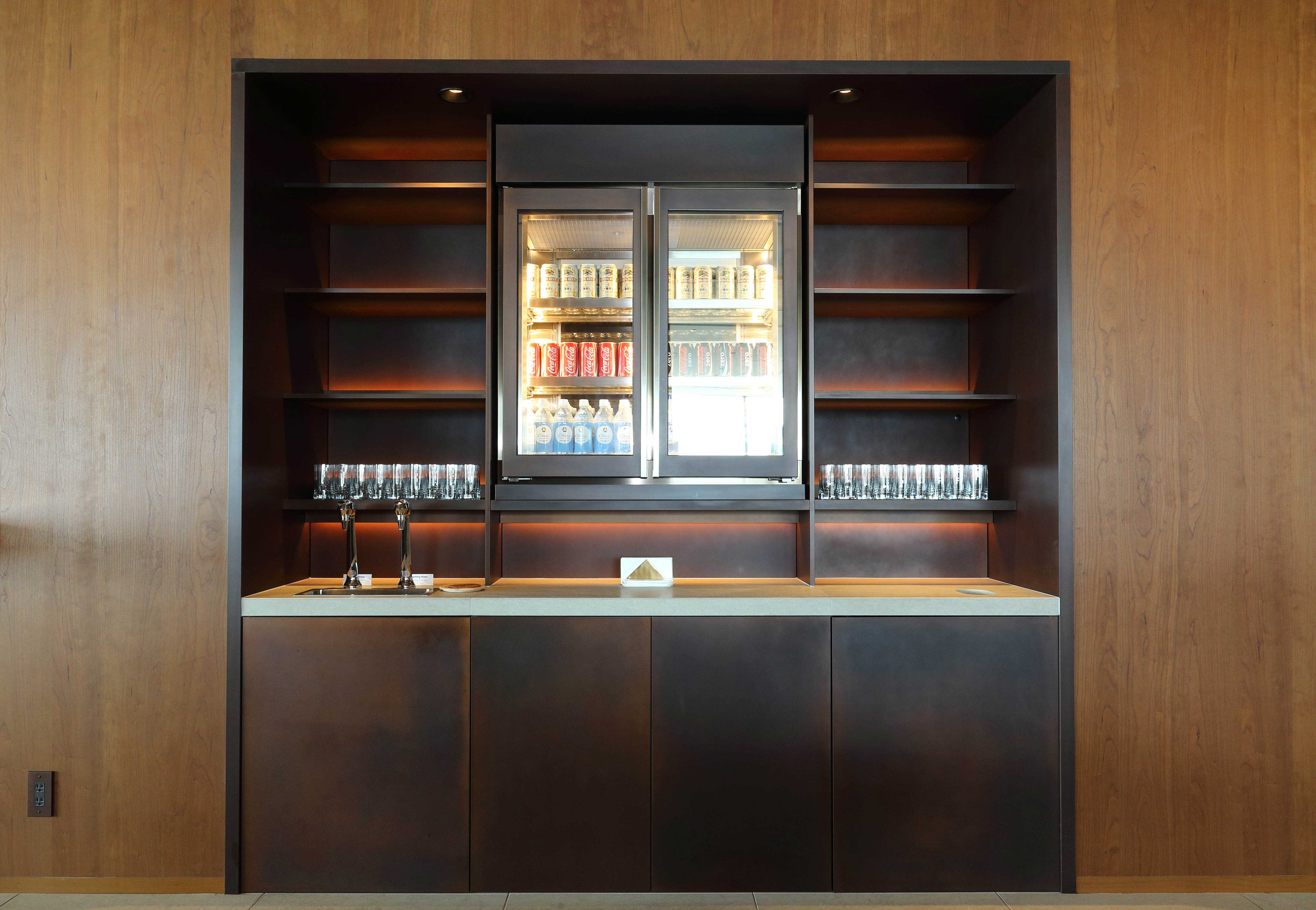
Sulfurized Bronze Counter
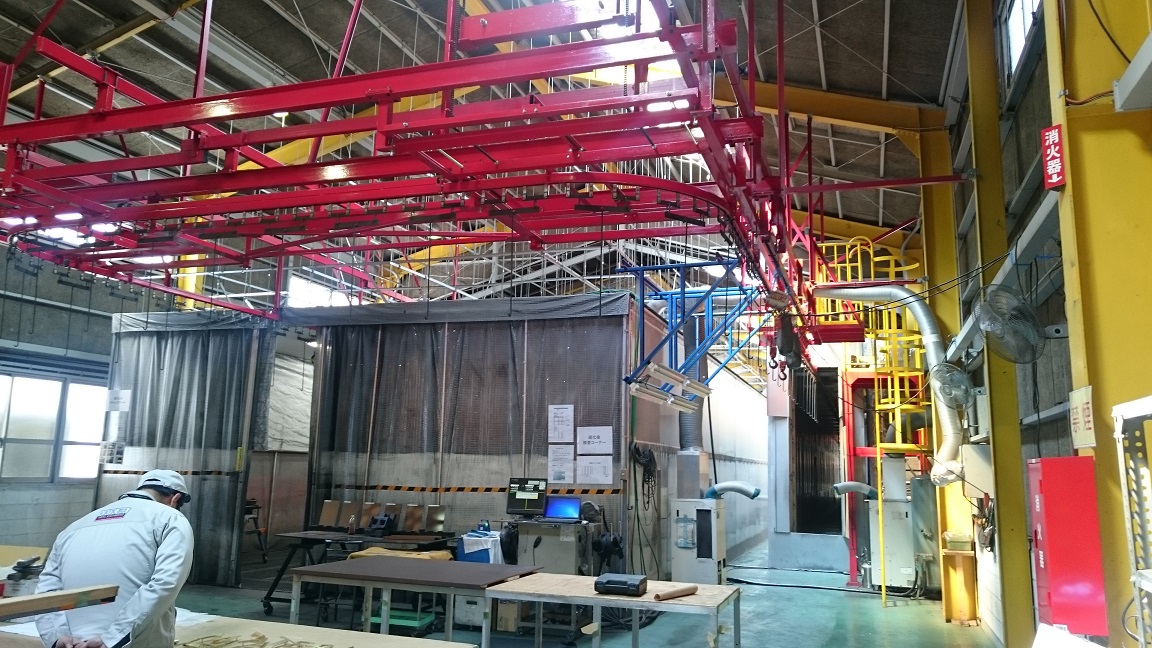
Sulfurizing Section
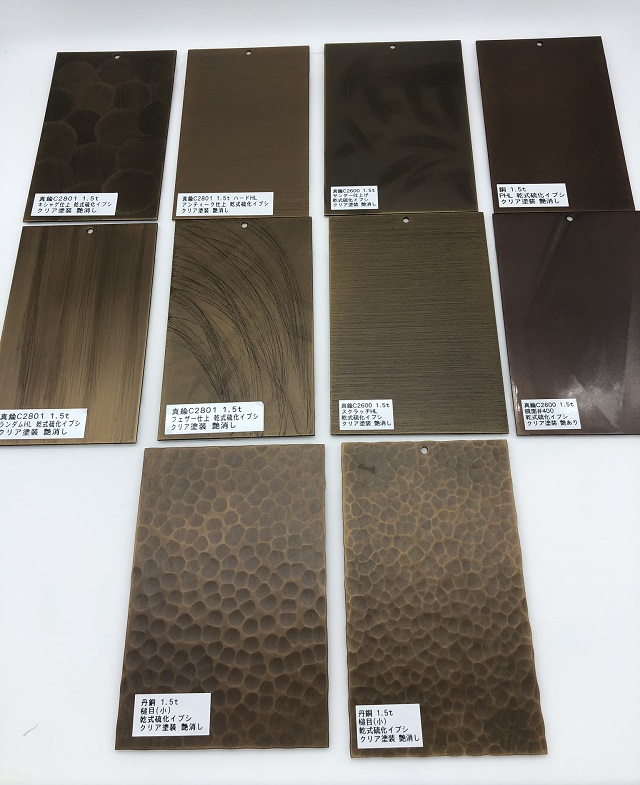
Sulfurized Bronze Alloys with Various Textures